Our Sales and operations team based in Hamburg have received praise from a customer for their dedication to customer service, quick thinking, and expert route planning and operations acumen which ensured continued delivery of a product allowing the customer to complete their full batch production and prevent a plant shutdown.
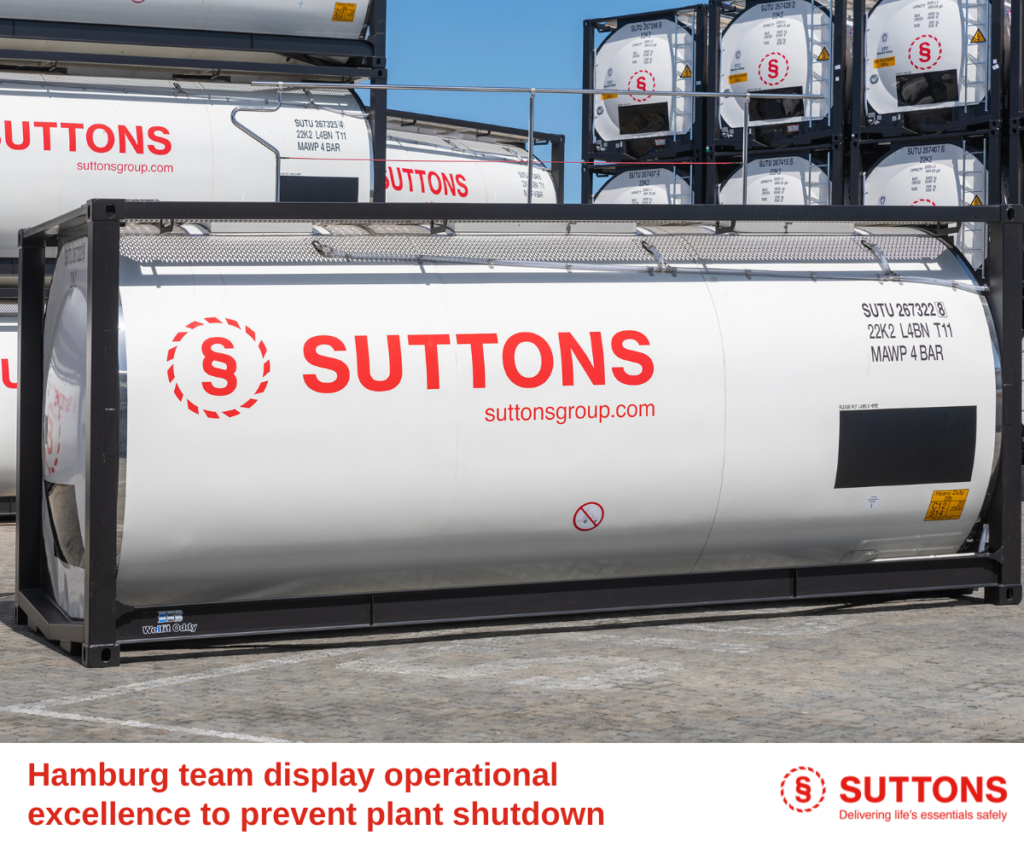
Our customer in Germany required an ongoing delivery campaign of 10 tanks over 10 weeks for a delivery location in Israel. This contract required tanks to be shipped from Antwerp on a weekly basis to the delivery point in Israel to meet an ongoing regular production schedule.
Due to factors outside of the customer or Suttons control, the final tank in the ten-week campaign faced a delay on its journey to Israel and wouldn’t make the scheduled delivery.
The Hamburg team worked tirelessly to find alternative transportation for the tank to overcome the delay and arrive in time to avoid the plant shutdown. They sourced an innovative rail solution through the Alpes to a port in Italy which then shunted the tank just-in-time to its destination. Resulting in a transit time of only 6 days compared to the expected 15, and no disruptions to the customers supply chain.
Plant shutdowns are very costly and have a large impact on supply chains, The team displayed fantastic commitment, customer service and operational knowledge to prevent this from happening.