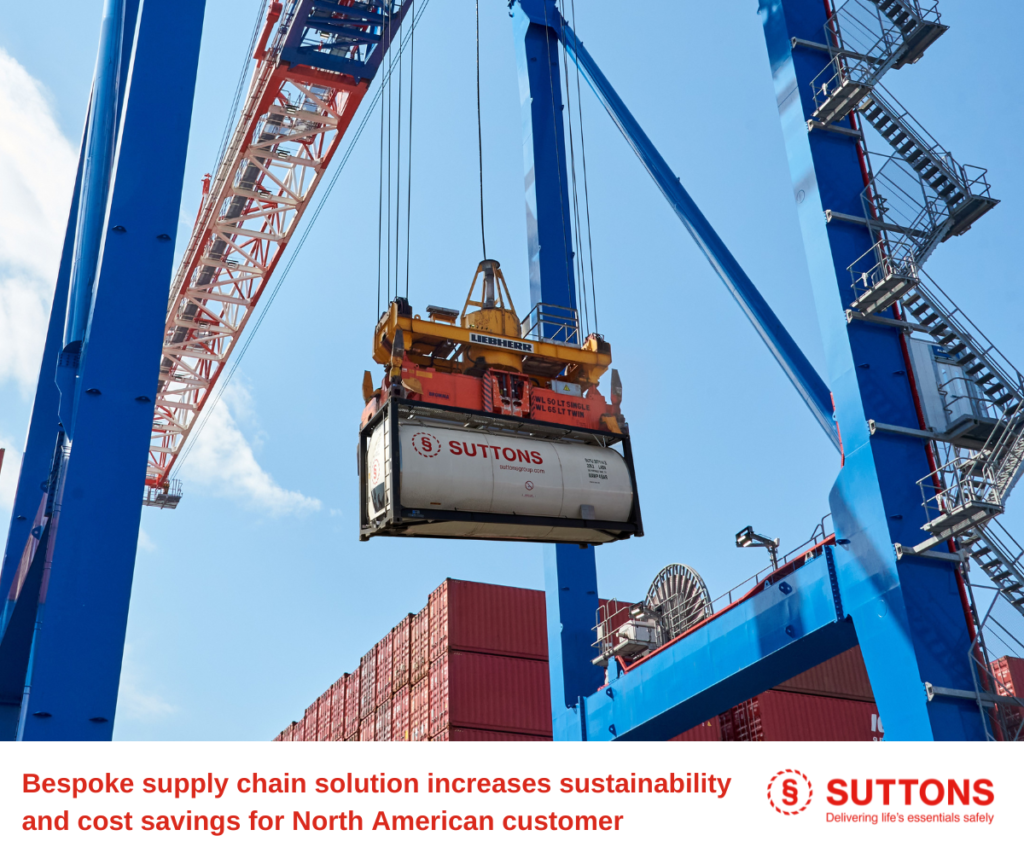
Suttons International North America is committed to continuous improvement and developing innovative solutions to meet their customer’s ever evolving supply chain requirements. The regional commercial team has recently delivered significant cost, reliability and safety innovations to a customer’s supply chain, while vastly reducing environmental impact through an innovative bespoke logistics solution.
The team has worked tirelessly with their leading fuel and lubricant additives customer to implement a rail-to-tank solution, which utilises a transload facility situated close to the desired shipping port. The solution combines the economic and environmental benefits gained from long distance domestic rail bulk transportation with the versatility of international intermodal tank container shipping.
Due to ongoing factors impacting the region such as port congestion for international shipping, driver shortages, and increased transportation costs, as well as a commitment to improving sustainability in their business and utilising their own fleet of rail cars, the customer required a solution to meet these unique needs.
The North American team worked closely with their customer, third party suppliers, and partners to understand the intricacies of the contract requirements when developing this bespoke solution.
The team found a rail facility close to the desired port free from the problems associated with
congestion and driver shortage, and a partner close by with the infrastructure to transfer from
rail to domestic tank trucks; although not familiar with tank containers, they were willing to work with the team to develop a rail-to-tank container transfer facility. Further investment was made to facilitate empty and loaded lifts as well as to provide full M&R capability. Finally, light weight trucks and chassis were sourced, which enabled the team to improve payloads for the customer by an average of 23%.
By increasing the payloads by 23% the team decreased the overall number of tank containers that they had to ship by the ocean by the same value. This advantage translated to savings in ocean freight coasts and further extended to reduction of inland trucking, storage, lifts and cleaning at the point of destination costs too.
The sustainability and environmental benefits were also significant thanks to the decrease in logistics miles. The team managed to reduced CO2 emissions and therefore the carbon footprint of the operations, as well as a reduction in the waste treatment streams associated with less tank containers being cleaned.
Thanks to the hard work of the North American commercial team, their customer has dramatically reduced their impact on the environment and implemented an effective cost saving measure to their supply chain.