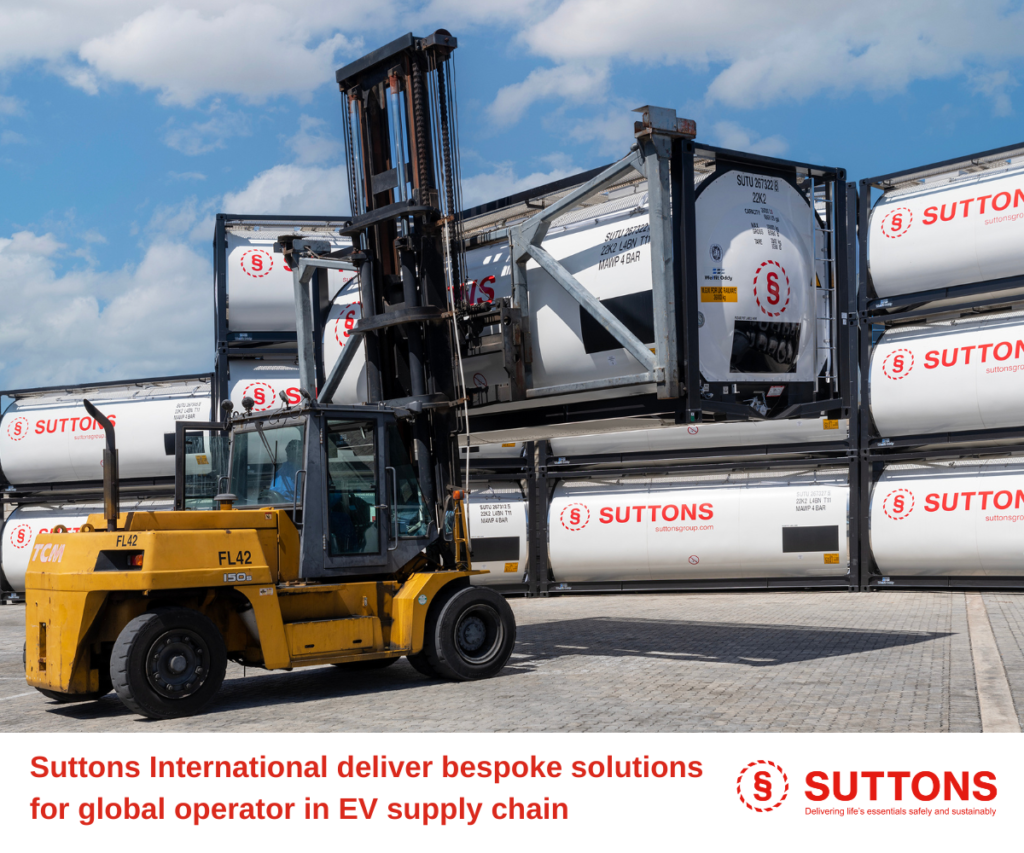
A prominent EV manufacturer who operates a Battery Manufacturing Gigafactory in Reno, Nevada, USA source electrolytes from South Korea as a vital component in the batteries that power their electric vehicles.
Collaborating with a Japanese partner, Suttons International tank containers are utilised to transport electrolyte solution from Busan, South Korea, to the Gigafactory in Nevada, USA.
The Gigafactory operates continuously using three production lines to support demand. Suttons and our Japanese partner provide dedicated support to one of these production lines, making accurate and on-time delivery crucial. Suttons are tasked with planning and managing the transportation of laden tanks over a significant distance, coordinating shipping, trucking, storage, and the return of empty containers back to Busan for reloading, on a continuous loop. The process requires close alignment between regional teams based in South East Asia and the United States to deliver consistently excellent customer service.
The Challenge
Just-in-time delivery requirements and the continuous flow of electrolyte required for battery manufacture presented operational challenges. To sustain the manufacturing process, an immediately available supply of electrolytes for call-off is required in proximity to the plant, and an efficient drop and swap procedure had to be implemented to achieve this.
The Solution
Operational planning teams overcame the challenge of requiring a continuous flow of electrolytes by identifying storage facilities in Stockton, CA, significantly reducing the distance for transport. On arrival at the Stockton depot, tanks are checked and either repressurised using Nitrogen or resealed while awaiting call-off from the plant.
Operational teams coordinated with a trucking partner to facilitate a process of swapping the laden tank and chassis at the production line with the empty tank on chassis. This seamless chassis exchange process takes approximately 45 minutes to complete.
Implementing these solutions has resulted in positive outcomes. Key performance indicators such as on-time delivery rates, fulfilment accuracy, and transit times significantly improved, reflecting a commitment to excellence.
The ability to develop and execute logistics solutions across a global supply chain underscores our expertise and dedication, with a focus on safety, sustainability, and delivering essential products.