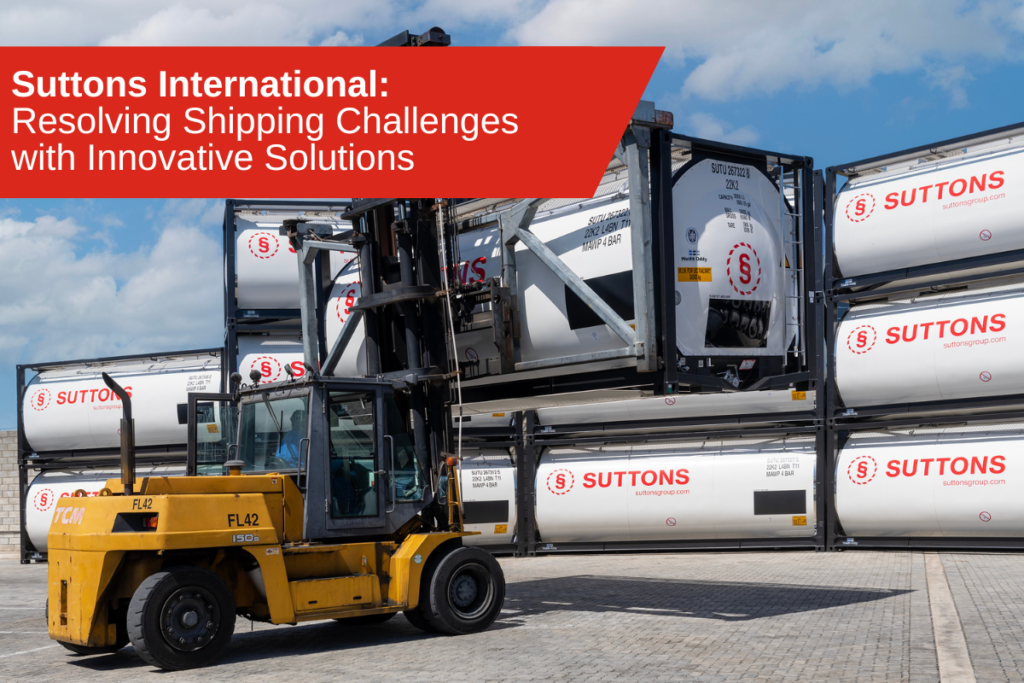
Suttons International stands out for its commitment to technical assurance, value, and sustainability. Recently, Suttons faced a challenge that threatened significant delays and added costs for customers. Thanks to the team’s technical expertise and proactive approach, these issues were effectively resolved, showcasing their dedication to customer satisfaction and operational excellence.
The Situation
Suttons International was tasked with shipping turpentine oil, a hazardous material with a pungent odour similar to rotten eggs. This product was being transported from Finland to Germany, and then onward to India. We deliver large quantities of this product from various global plants across Europe to destination in India and its use is crucial for the perfume and fuel industries.
During a transhipment at the terminal in Germany a strong smell was detected. The port authority, unable to determine the cause of the odour, halted the tank. Although the odours from turpentine oil are noticeable, they pose no harm to human health. However, any odour detection prompts a precautionary process to identify the source in the instance of a damaged tank or a leakage. Such incidents typically require immediate intervention by the local Fire Department and a third-party review, costing up to €5,000 and causing significant delays.
The Challenge
The core issue was the odours which are released from the tank. This harmless and normal process unfortunately prompts port authorities to investigate due to being unable to differentiate whether the smell originated from a damaged / untight gasket or a leaking tank. This resulted in tanks being stopped, isolated in safe zones, and subjected to costly and time-consuming reviews.
Suttons’ Solution
Suttons International leveraged their deep industry knowledge and proactive approach to devise a robust solution:
Gasket Review and Upgrade: Suttons initiated a comprehensive review of the gaskets used in their tanks. They proposed using gas tight-gaskets, which, although not the industry standard, provided a higher level of sealing. This preventive measure, despite incurring additional costs, significantly reduced the risk of odour-related stops.
Eco-friendly Seals: The previous seals that were replaced were classified as PFAS products, which are Persistent Organic Pollutants (POPs) and are concerning due to their persistence in the environment and harmful properties. The new replacement seals do not contain these harmful substances, making them more eco-friendly.
Customer Communication: Educating customers about the importance of higher-standard gaskets was crucial. Suttons explained the benefits, including the prevention of product blacklisting and ensuring the reliability of shipments.
Stakeholder Education: Suttons also took steps to educate production plants and logistics partners about the necessity of these gaskets. They facilitated the supply of upgraded gaskets, emphasising their role in minimising risks and ensuring smooth operations.
Environmental Benefits: The upgraded gaskets also offered environmental advantages by reducing the need for tank shunting, emergency callouts, and the cleaning chemicals used to detect spills and leaks, thereby contributing to sustainability efforts.
Impact and Outcome
The proactive measures taken by Suttons International yielded impressive results. Since the implementation of the gas tight-gaskets, there has been only one incident of a tank being blocked, and that was due to an unrelated spill during loading. Prior to this change, eight tanks were stopped within a six-month period.
This significant reduction in blocked tanks not only improved operational efficiency but also resulted in substantial cost savings. The enhanced reliability and safety of shipments strengthened Suttons’ reputation as a customer-centric and innovative logistics provider. Additionally, the environmental benefits underscored Suttons’ commitment to sustainability.